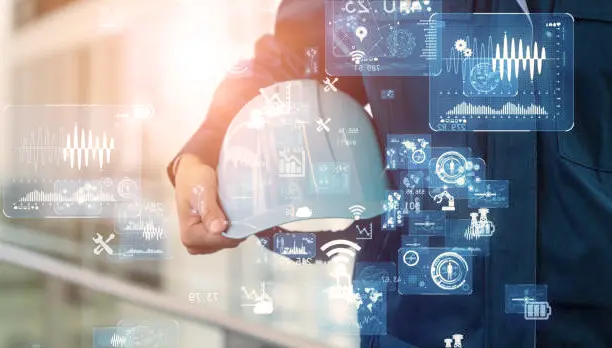
The Evolution of Robotics in Manufacturing: From Automation to Collaboration
- Admin
The manufacturing industry has undergone significant transformations with the integration of robotics technologies. From traditional automation to collaborative robots (cobots), robotics has revolutionized production processes, leading to increased efficiency, flexibility, and safety. This article explores the evolution of robotics in manufacturing and its implications for the future of the industry.
Traditional Automation in Manufacturing:
Robotic Automation: Traditional industrial robots have been widely used in manufacturing for decades, performing repetitive tasks such as welding, assembly, and material handling. These robots are programmed to operate within predefined parameters and are typically separated from human workers to ensure safety.
Benefits of Robotic Automation: Robotic automation offers numerous benefits to manufacturing operations, including increased productivity, improved product quality, and reduced labor costs. By automating repetitive and hazardous tasks, robots enhance efficiency and create safer working environments for employees.
Introduction of Collaborative Robots (Cobots):
Collaborative Robotics: Collaborative robots, or cobots, represent a new generation of robotics designed to work alongside human workers in manufacturing settings. Unlike traditional industrial robots, cobots are equipped with advanced sensors and safety features that allow them to operate safely in close proximity to humans.
Benefits of Cobots: Cobots offer several advantages over traditional industrial robots, including increased flexibility, easier programming, and lower implementation costs. By collaborating with human workers, cobots enable greater adaptability and agility in manufacturing processes, leading to improved productivity and responsiveness to changing production needs.
Applications of Robotics in Advanced Manufacturing:
3D Printing: Robotics technologies, including robotic arms and gantry systems, are used in additive manufacturing processes such as 3D printing. Robots can precisely deposit layers of material to create complex geometries, prototypes, and customized parts with high accuracy and repeatability.
Machine Tending: Robotics automation is extensively used in machine tending applications, where robots load and unload parts from CNC machines, lathes, and milling machines. Automated machine tending reduces cycle times, minimizes downtime, and improves overall equipment efficiency (OEE) in manufacturing operations.
Future Trends in Robotics and Manufacturing:
AI Integration: The integration of artificial intelligence (AI) with robotics is expected to drive further advancements in manufacturing automation. AI algorithms enable robots to learn from data, adapt to changing environments, and make autonomous decisions, enhancing their capabilities in complex manufacturing tasks.
Human-Robot Collaboration: The future of manufacturing will likely see increased collaboration between humans and robots, with a focus on shared workspaces and task-sharing arrangements. Collaborative robots will play a central role in creating flexible, adaptive manufacturing environments that combine the strengths of human ingenuity with robotic precision and efficiency.
Conclusion:
The evolution of robotics in manufacturing represents a paradigm shift in how products are produced and assembled. From traditional automation to collaborative robotics, robots have become indispensable tools for enhancing efficiency, quality, and safety in manufacturing operations. Looking ahead, the integration of AI and human-robot collaboration will continue to drive innovation and shape the future of manufacturing in exciting ways.
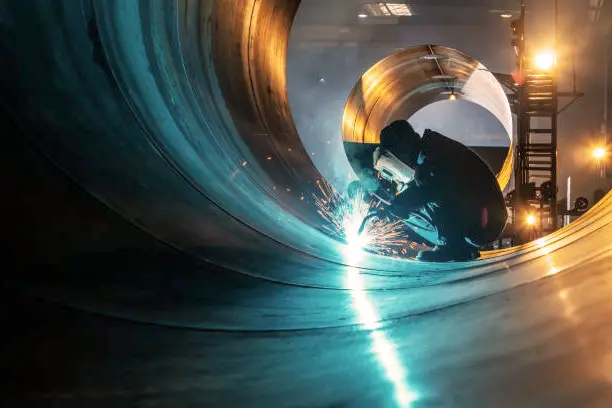